I've always preferred the hit of a big pin. For some reason,
it just seems more intimate. I like intimate.
Not too long ago, your big pin choices were 3/8-10 or 3/8-11. Then
Uni-Loc introduced the Radial pin which was quickly embraced by many
cuemakers. It had several advantages over the competition.
The threads cut into the wood were much cleaner since less wood was
being removed by the tap. And a .3125" pilot allowed the tap to
follow more accurately the bored lead hole. Maintaining
concentricity, a common problem with the big pins, suddenly became
achievable by anyone. And lastly, the snug, intimate fit between
the pin & the shaft was a reassuring promise that the wooden threads
would last a long time.
I built several cues using the Uni-Loc Radial pins & considered making
it my new standard. However, virtually every cue I sold previously
had 3/8-10 pins. I hated to switch & be forced to carry spare
shafts with 2 different threads.
I found a machinist who made 3/8-10 pins that had a slightly different
thread form than the standard 60° V form. His modified pins
located the shaft on the minor diameter of the pin rather than the pitch
diameter of the standard pins.
This made achieving concentricity
as easy as boring a true hole in your shaft. You were no longer
penalized if your tap wandered - as they tend to do. And, as
above, the snug, intimate fit between the pin & the shaft was a
reassuring promise that the wooden threads would last a long time.
And it meant that my
new cues & shafts would be compatible with my old ones. I liked
that idea.
Since 2006, almost every cue I've built has the new modified 3/8-10 pin,
sometimes called the Flat Bottom or FB pin. I've had great success
with it & many other cuemakers are using it now, too. I published
a picture of a cutaway shaft, showing the differences between the
standard pin & the modified pin. Apparently, it was a convincing
argument because sales of the modified pin increased greatly after the
picture appeared. I took it down after a few years because the
modified pin appeared to be well recognized & its benefits understood
universally.
However, it seems that a new generation is asking questions again.
I decided to put this page up again with the original picture and an
updated one, too. I was fortunate enough to find the original
sample piece used in the picture. It has darkened with age but it
was satisfying to find it still laying around. And rather than go
thru the explanations again, just click on the pictures & the
explanations are there for you.
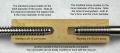
This is the original picture that I published in 2006.
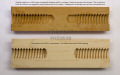
This picture shows that original blank above a new version. I find
it an interesting "blast from the past" but it's also a statement about
the difference between regular drilling & tapping compared to live
tooling. However, I must admit it is not a fair comparison.
The original sample is actually a very nice piece of curly maple that I
had laying around for use in JP's. The problem is that highly
figured wood doesn't tap cleanly. Since the original picture was
designed to show thread fit, I wasn't too concerned that the threads
themselves would be less than stellar. Still...
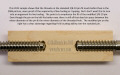
Finally, an updated version of the original.
Regarding questions about the backwards compatibility - when I used the
std 3/8-10 pin, I bored my shafts to .302" diameter before running a tap
into it. This was a smaller hole than most used. I liked it
because the pin had a tighter fit. Again, there's that intimacy I
like. The problem arises because the modified pin has a .308" minor
diameter & will not fit into an older shaft unless the .302" diameter is
enlarged to .308". It takes about 2 minutes to set it up & run a reamer
into the existing hole.
PLEASE NOTE:
Most standard or aftermarket 3/8-10 shafts will fit without further
modification. They are usually bored/drilled to .3125" diameter &
will have plenty of clearance for the FB pin. However, tapped
threads are not as clean as live tooled threads. To
correct combat this, some builders soak
the threads with cyanoacrylate (CA) both before and after tapping to
strengthen the torn wood & snug up the fit. This
after-the-fact attempt at "precision" will make the shaft fit nicely
on a std pin but can be too tight on a modified pin. Again,
running a tap and/or a reamer into the hole will solve the problem.
Other things I've noticed:
Laminated shafts do not tap as cleanly as solid shafts.
Production shafts with inserts seem to a dull tap quickly.
Production shaft manufacturers are slow to replace a dull tap.